Temperature changes prior to engineered wood install
6 years ago
Featured Answer
Sort by:Oldest
Comments (14)
Related Professionals
Dorchester Flooring Contractors · Elgin Flooring Contractors · Oregon City Flooring Contractors · Pearland Flooring Contractors · Shepherdsville Flooring Contractors · St. Louis Flooring Contractors · Baldwin Tile and Stone Contractors · Dothan General Contractors · Jeffersonville General Contractors · Marinette General Contractors · Millbrae General Contractors · Modesto General Contractors · Newington General Contractors · North Smithfield General Contractors · Avenal General Contractors- 6 years ago
- 6 years ago
- 6 years ago
- 6 years ago
- 6 years ago
Related Stories
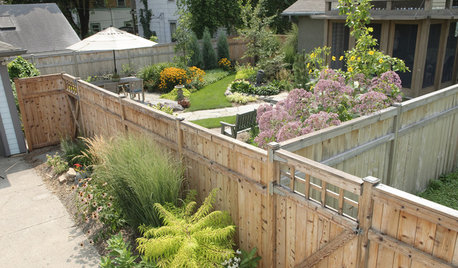
FENCES AND GATESHow to Install a Wood Fence
Gain privacy and separate areas with one of the most economical fencing choices: stained, painted or untreated wood
Full Story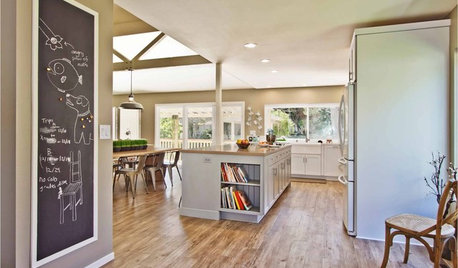
FLOORSWhat's the Right Wood Floor Installation for You?
Straight, diagonal, chevron, parquet and more. See which floor design is best for your space
Full Story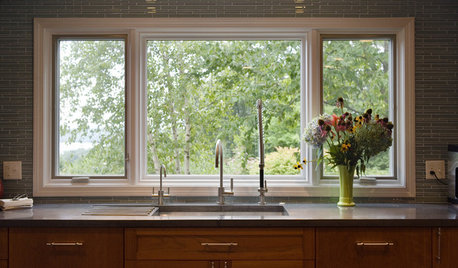
WINDOWSContractor Tips: How to Choose and Install Windows
5 factors to consider when picking and placing windows throughout your home
Full Story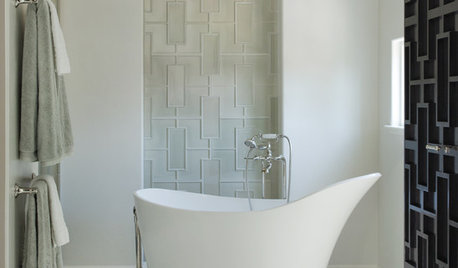
REMODELING GUIDESContractor Tips: How to Install Tile
Before you pick up a single tile, pull from these tips for expert results
Full Story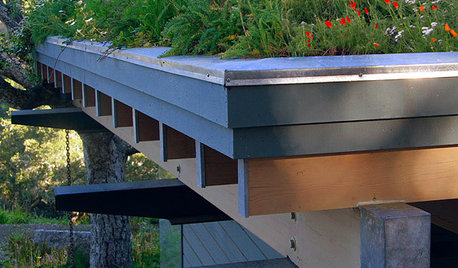
EARTH DAYHow to Install a Green Roof
Covering a roof with low-maintenance plants has benefits beyond just beauty. Get the details here
Full Story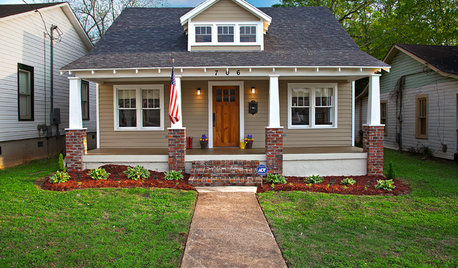
MATERIALSThe Most Popular Roofing Material is Affordable and Easy to Install
Asphalt shingles, the most widely used roof material in the U.S. are reliable and efficient, and may be right for you
Full Story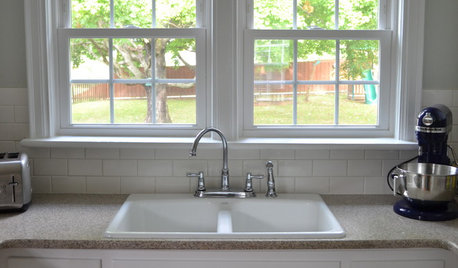
KITCHEN BACKSPLASHESHow to Install a Tile Backsplash
If you've got a steady hand, a few easy-to-find supplies and patience, you can install a tile backsplash in a kitchen or bathroom
Full Story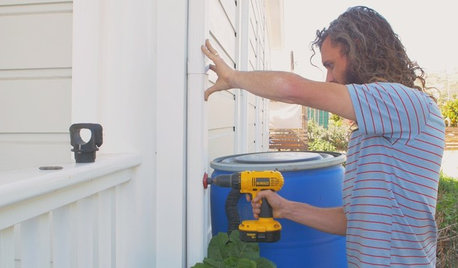
HOUZZ TVHouzz TV: How to Install a Rain Barrel
This DIY tutorial shows how easy it can be to capture rainwater from your roof to use in your garden later
Full Story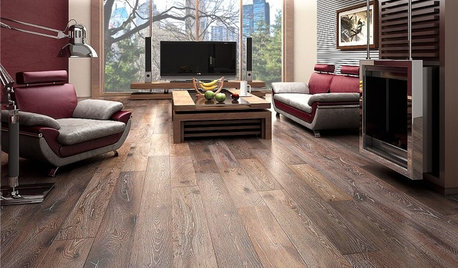
REMODELING GUIDESWhen to Use Engineered Wood Floors
See why an engineered wood floor could be your best choice (and no one will know but you)
Full Story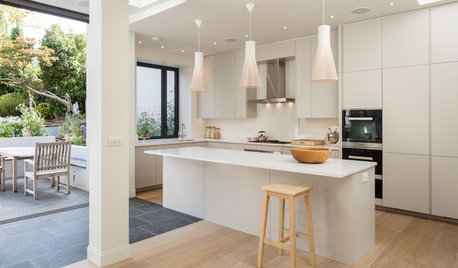
FLOORSHow to Care for Engineered Wood Flooring
Keep your wood floor looking its best with these tips and tricks from the experts
Full Story
millworkman