Insulation - some advice
15 years ago
Related Stories
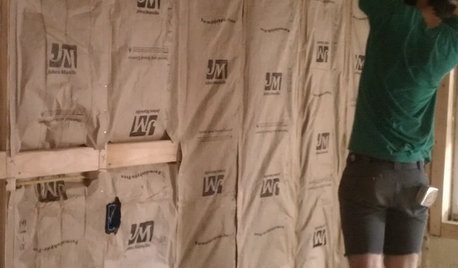
REMODELING GUIDESCool Your House (and Costs) With the Right Insulation
Insulation offers one of the best paybacks on your investment in your house. Here are some types to discuss with your contractor
Full Story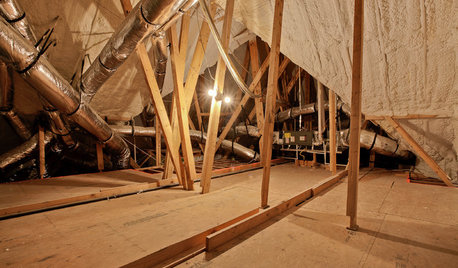
GREEN BUILDINGEcofriendly Cool: Insulate With Wool, Cork, Old Denim and More
Learn about the pros and cons of healthier alternatives to fiberglass and foam, and when to consider an insulation switch
Full Story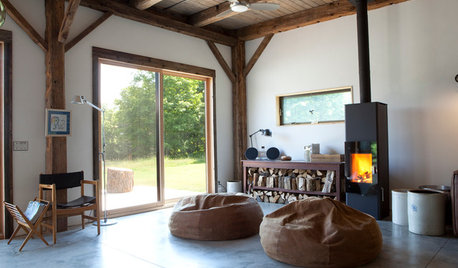
GREEN BUILDINGInsulation Basics: Heat, R-Value and the Building Envelope
Learn how heat moves through a home and the materials that can stop it, to make sure your insulation is as effective as you think
Full Story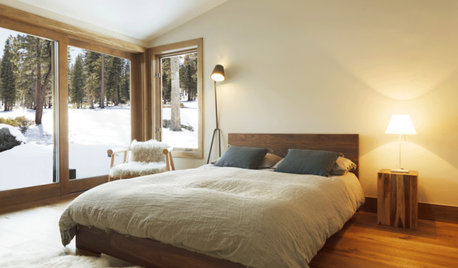
WINDOW TREATMENTSEasy Green: 9 Low-Cost Ways to Insulate Windows and Doors
Block drafts to boost both warmth and energy savings with these inexpensive but effective insulating strategies
Full Story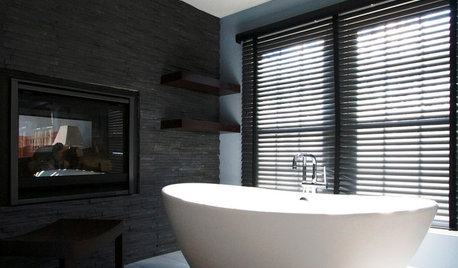
BATHROOM DESIGNDreaming of a Spa Tub at Home? Read This Pro Advice First
Before you float away on visions of jets and bubbles and the steamiest water around, consider these very real spa tub issues
Full Story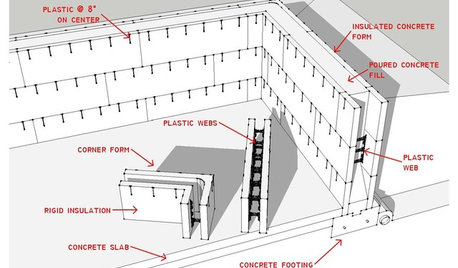
KNOW YOUR HOUSEKnow Your House: The Basics of Insulated Concrete Form Construction
Get peace and quiet inside and energy efficiency all around with this heavy-duty alternative to wood-frame construction
Full Story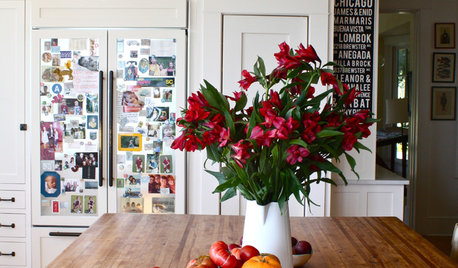
DECORATING GUIDES10 Design Tips Learned From the Worst Advice Ever
If these Houzzers’ tales don’t bolster the courage of your design convictions, nothing will
Full Story
REMODELING GUIDESContractor Tips: Advice for Laundry Room Design
Thinking ahead when installing or moving a washer and dryer can prevent frustration and damage down the road
Full Story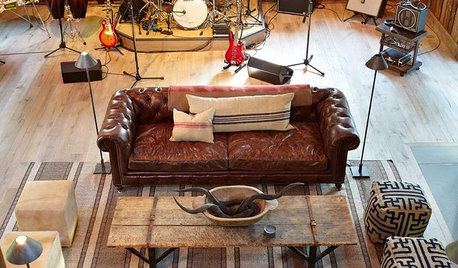
THE ART OF ARCHITECTURESound Advice for Designing a Home Music Studio
How to unleash your inner guitar hero without antagonizing the neighbors
Full Story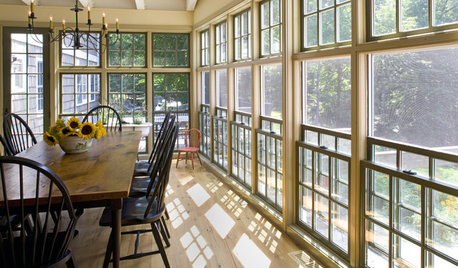
HOUSEKEEPINGLower Your Heating Bills With Some Simple Weather Stripping
Plug the holes in your house this winter to make sure cold air stays where it belongs: outside
Full StoryMore Discussions
worthy
bdpeck-charlotte
Related Professionals
Corpus Christi Architects & Building Designers · Enterprise Architects & Building Designers · South Elgin Architects & Building Designers · Wilmington Home Builders · Royal Palm Beach Home Builders · Clinton General Contractors · Coshocton General Contractors · Dunedin General Contractors · Keene General Contractors · Parkville General Contractors · Reisterstown General Contractors · Rock Island General Contractors · Saint Andrews General Contractors · Sterling General Contractors · Waianae General Contractorsmightyanvil
doogan123Original Author
sierraeast
bungeeii
energy_rater_la
doogan123Original Author
rollie
bungeeii
doogan123Original Author
doogan123Original Author
rollie
doogan123Original Author
worthy
rollie
doogan123Original Author
worthy
rollie
doogan123Original Author
rollie
doogan123Original Author
rollie
doogan123Original Author
rollie
arewethereyet
rollie
energy_rater_la
missleah
worthy
sierraeast
sierraeast
sierraeast
worthy
Ron Natalie