Closed cell foam - is it worth spending additional $5500?
I�m trying to understand if going with an entirely spray foamed house for ~$5500 more is worth the extra cost or not. Hopefully some of you can help me understand the potential ROI. Thanks in advance!
Here�s some details
Heating �
forced air natural gas high efficiency ~96%
cost/ Therm = ~$0.63 (guessing this will rise but who knows by how much per year)
House -
~3500 sq ft two story located in Minneapolis, MN
~1500 main floor, ~2000 2nd floor, extra space coming from living area above the garage
10� ceilings on main floor
9� ceilings in basement and 2nd floor
Basement will be unfinished for the time being
House will be built in a residential area with moderate tree coverage
2 adults, 2 kids (3 and 5 now)
Anticipated utilities
Winter months - $300+
(average in old house was ~$250)
Summer months - $150+
(average in old house was ~$100)
based off my current house which isn�t insulated as well but is smaller (~2000 sq ft above ground)
Current insulation plans
Walls � 2x6 with Blown in fiberglass to give R-21
Ceiling � thin layer of closed cell foam to seal ceiling, blown insulation over closed cell overall R-44
Basement � foil faced foamed placed on basement wall R-15 (not sure exactly on this)
Cost to insulate to this plan - ~$12k
All spray foam for above grade walls and ceiling � $17.5k
Can you help me understand if spending the extra $5500 is worth it? Any idea on the payback period? I�m aware of some of the other benefits of foam over just R value like air sealing and the benefits that offers.
Thanks!
Comments (27)
mrspete
10 years agoWow, that's a lot of money. Let's math:
I'm going to assume that you'll have 6 months of summer and 6 months of winter -- that may not be true. So, if your assumptions are correct about the $300 (x 6 months) and $150 (x 6 months) power bills, you're looking at paying $2,700 total in power each (that sounds like an awful lot of money for power).
And now I'm stuck . . .
I was going to figure up how many months it'd take you to save the extra $5500, but I don't know how much you'd save each month by going with the extra insulation.
The answer cannot be determined with the current information only.
energy_rater_la
10 years agoyou'll never get your money back using spray
foam in walls.
much better option is to use foam sheathing
to exterior of walls. tape all seams, seal all penetrations
this will add R-7, if
you purchase the high insulation foam sheathing.
adding R-7 to the R-19 will give you R-26.seal sole plate to slab or subfloor with double
layer of caulk or sill seal.
use air tight drywall approach for interior.this is an efficient affordable high performance wall.
here in the south we foam the roofline because
we do stupid stuff like putting equipment & ducts
in the attic.
if your ducts and equipment are not in attic,
think about just putting a couple of inches
of cc foam on attic floor (and any kneewalls)
then blow conventional insulation to reach
desired R-value.note that with foam...the code mandated R-value
has to be installed. no 'average fill" that varies
from 1/4" to 3"...no 'performs as Rxxx" it has to
be Rxxx.actually $5500 isn't bad, but it makes me really
question depth and quality of install.best of luck
Related Professionals
Gladstone Architects & Building Designers · Aurora General Contractors · Clinton General Contractors · Dardenne Prairie General Contractors · East Riverdale General Contractors · Hillsboro General Contractors · Keene General Contractors · Lake Forest Park General Contractors · Los Lunas General Contractors · Miami Gardens General Contractors · Modesto General Contractors · Mount Laurel General Contractors · Mountain View General Contractors · San Marcos General Contractors · Signal Hill General Contractorskwoody51
Original Author10 years agoI realize I don't have the information about the amount to be potentially saved and thus calculating the ROI, hence my question. I didn't know if anyone had some insight into the potential reduction in utilitiy bills with CC foam vs regular blown in insulation.
I talked with the builder about putting a 1" XPS sheet on the outside of the OSB. He didn't seem too thrilled about it. Main issue being trying to adhear the siding to it, increased labor for install and dealing with moisture management between the XPS and the OSB.
His point seemed valid hence my looking into spray foam vs XPS on the exterior.
Happy to hear any counter points that address installing cement board over the XPS and moisture control between the XPS and OSB (condensation mainly during colder months).
energy_rater_la
10 years ago"I talked with the builder about putting a 1" XPS sheet on the outside of the OSB. He didn't seem too thrilled about it. Main issue being trying to adhear the siding to it, increased labor for install and dealing with moisture management between the XPS and the OSB."
builder probably hasn't ever done thistype of install.. but it isn't rocket science. moisture management isn't an issue, if furring strips are installed to nail cement board to. a little extra labor, cheap materials. if he doesn't want to spring for the furring strips, use longer nails & set nail depth on nail guns.
in the foam sheathing,
seams are taped, any holes are sealed prior to cladding.
the foam sheating becomes both air & vapor barrier.
if he is truly worried, he can install house wrap over foam sheathing...or next to studs.
waste of $$ & labor...but just a few hundred.with foam to exterior you get a thermal break
for wall studs. wood is R-1 per inch, so your
2x6 has R-5.5 R-value, this derates insulation
in walls R-value. can't tell you exactly how much
because my computer program does the calc."His point seemed valid hence my looking into spray foam vs XPS on the exterior. "
not much validity to his point, but by passing it off
to foam insulator to improve R-value of wall instead
of understanding how & why to do this.this assembly isn't just something I made up, my
local utility co-op & I have promoted this for years
as an important step in efficiency.
buildingscience.com calls the assembly I described
in post above as the perfect wall...for all climates.
one can't do much better
than that...if you/he has the want to do it. if not...it
will never get done.as for costs of your foam quote....
what does the bid say exactly?
how many inches of foam for walls?
how much for roofline..or is it attic floor?
what is insulation depth spec'd on the
quote. in their words.we don't use cc foam here, except under floors in crawlspaces. our foam is open cell.
It has been years since I did a whole house foam
calc..(walls & roofline) but ROI for the 2500 sq ft
house was 25 years.
once I took walls out of the calc, the roofline
install dropped to 5 or 6 years.
note that we usually have 8 months of cooling
in La. (not now...got sleet/snow on the ground)I'm really curious about the foam bid.
can you share it?
are you really looking for options or
just the ok to go with what you've been
offered?
sometimes the homeowner has to say...
this is what I want...without that, the
builder will do what he has done
for years.best of luck.
Annie Deighnaugh
10 years agoWe went with closed cell and are happy. In addition to the great insulation and the structural rigidity, and waterproof, and no need for vapor barrier, it has made the house very quiet as it is very sound deadening. Yes it was very expensive, and you can't run wires through exterior walls easily, but we are glad we did it. Everything we read about going green said but your money into insulation...regardless of how you generate a BTU, the longer you hang on to it, the better.
kwoody51
Original Author10 years ago1st up - thanks for all the great information!
2nd - I should have mentioned that we are already in construction. The 1st floor and garage are currently getting sheathed as we speak. They will start framing the 2nd floor next week, assuming the weather isn't crazy cold.Based on the above we are moving forward with stick built, no ICF's.
As for rigid foam over the sheathing, I'm not opposed to it but this is my worry - http://www.greenbuildingadvisor.com/blogs/dept/musings/calculating-minimum-thickness-rigid-foam-sheathing
This article suggests that I'd have to go with foam sheathing of ~4" or more based on my zone 6 location.
4" of foam over the sheathing is much more expensive and hard to install over vs just 1" of foam.
My comment about moisture management earlier had to due with sorption, as highlighted in the link, not drainage issues due to improper flashing or joint taping.
We are also past the point to put up insulated panels, as mentioned boards are going up as we speak. So my options as I know them are
1. Closed cell foam in the wall
2. Rigid foam over the sheathingI don't have the CC foam quote, I asked the builder for the up charge and that's where the $5500 came from. Can't provide you with anymore verbiage about it other than the cost at this time.
Thanks again and keep the info flowing!
darleneac59
10 years agoWe were planning on using spray foam since we plan on living in our home for a very long time we felt we would get our money out of it. When my husband started researching it he became concerned about the off gassing. Has anyone else had concerns about this?
Annie Deighnaugh
10 years agoWith our closed cell, it did give off an odor when it was done and for several days after that, but once the stuff cured and the walls were closed in with sheet rock, no smell at all.
If you do go with spray foam, be sure to box in any in-wall speakers you might have so they don't get foamed in, and our security guy screwed up, even though we told him we were spray foaming the walls...his wires got buried and now we have all battery operated sensors on our windows...PITA.
worthy
10 years agoDone right, the ccspf will work well--at great cost. And likely producing a lower whole wall R value than sheathing in foam board with fibrous insulation or cellulose between the studs.
As energy rater says, two inches of board will do in US climate zone 6. (Polyiso boards have a higher per inch R value than XPS and will likely meet the IRC values.)
I sheathe 2x6" framing in one-inch XPS in what's equivalent to US Zone 5--Toronto GTA, Canada.) And, FWIW, John Straube of Building Science Corp. agreed that that is sufficient in our climate.
Your builder's inexperience in sheathing is unfortunate. Furring and/or long screws are all that's necessary.
One-inch extruded polystyrene board over 2"x6" framing in cold zone construction. Photo: Heather Joy Investments Ltd.
kwoody51
Original Author10 years agoVery interesting artical! I was leaning toward XPS but it was only from a cost perspective guess it has some other benefits as well!
I'm happy to talk to the builder more about XPS and this information is helpful. I do have a few more questions.
Can you help me understand the install process for the XPS? Is it glued to the house or nailed? I assume it goes right onto the sheathing.
Once up the seems are then taped?
Then the siding is nailed through the XPS to the sheathing below?
Does the XPS act like a house wrap now?
My builder highlight a concern about the cemet board potentially being "wavy" due to having a flexible undermounting surface. Any truth to this?
Once the XPS how do you create a drainage plane between it and the cement boards? I assuming this what the furring strips help with, are the necessary?
Thanks again for all the help! I fully recognize its a do it now or never do it type of decision hence all the help is great!
Thanks!
energy_rater_la
10 years agoCan you help me understand the install process for the XPS? Is it glued to the house or nailed? I assume it goes right onto the sheathing.
nailed. 4-6" on edges, 8" in the field of the sheathing.
Once up the seems are then taped?
yes. prior to cladding any holes are also sealed.
Then the siding is nailed through the XPS to the sheathing below?
yes.
Does the XPS act like a house wrap now?
yes. but some builders are uncomfortable with this. in my
area they are ok with wasting client's $$ with house wrap
on studs..or osb/cdx..then foam sheathing. extra work, labor & materials. totally unnecessary if foam sheathing is sealed.My builder highlight a concern about the cemet board potentially being "wavy" due to having a flexible undermounting surface. Any truth to this?
not if nail guns are set correctly & the correct
fastener is used & fastner is correct length.when nail gun depth is not set correctly to allow for nail
to penetrate foam sheathing to set into osb/cds or
studs then the nail doesn't hold. all nail guns
have settings..they just need to be set correctly
& kept on that setting for totality of cladding install.
if the nail isn't long enough..it doesn't hold.when these things aren't done properly the siding
can look wavy. I see it more with vinly...don't think
I've seen it with hardi type products.Once the XPS how do you create a drainage plane between it and the cement boards? I assuming this what the furring strips help with, are the necessary?
personally I perfer furring strips...but not for drainage.
think about it for a minute.
tyvek installed tightly on osb...hardi installed on top..
drainage..where?
so then tyvek on osb..or not...foam sheathing with
hardi on top...foam is drainage plane.it isn't stucco..which requires a bond break.
glad that you've taken time to understand why
this is important. spray foam is often used as
an easy out for builder. but it isn't the fix all
that it is believed to be. it has it's place...
but IMO walls are not the place!best of luck.
kwoody51
Original Author10 years agoThanks again!
Builder asked about doing a 1" or 1.5" XPS vs the 2". What risk am running if I go thinner than 2". I want to get the benefit while imposing the least expense and effort to adding it.
I assume I will still have a vapor barrier installed between the drywall and the studs in the house.
I'm sure that my builder is trying to balance out trimming out the windows if we got to 2" XPS thought I read something about 2" requiring some special strapping and window trimming techniques.
I know I'm WAY over thinking this but my engineering (mechanical) brain has me running through long forgotten thermodynamics and heat transfer classes. I just want to flip to the back of the book and get the answer :)
Seriously though I do like and want to understand how it works. It just seems there is a lot of info and some is slightly different.
So to summarize from inside out
Drywall
6mil poly
Blown insulation
OSB sheathing
House wrap (may not be needed if XPS is sealed)
XPS (thickness 1" or more)
Furring strips (optional - what do I loose if these aren't added)
Siding of choice (LP smart side in my case)energy_rater_la
10 years agoyou should have warned me up front you were
an engineer. (LOL!)go back & read the article, from what I got
with the xps there is no interior vapor barrier..
no poly behind sheetrock.
the walls have to dry to either outside
or insde. with xps on exterior there
will be no drying out of the wall..if xps
is done right, so drying has to occur to interiorjust like here in the south..no interior vapor
barriers, no enamel paints, vinly wall papers
or poly.double check me...but thats what I got.
personally I like furring strips because we
often use a foil faced foam sheathing.
facing the foil to wards cladding.
this acts as a radiant barrier to reflect
heat out of walls, with the 3/4" air
space provided by furring strips.
radiant barriers provide little savings in
cold climates, it is a hot climate product.otoh the furring strips will provide a solid surface
for hardi ( I call all brands hardi...just what it is)
to be attached to. without it, if you want to nail
through into studs. you have to pop lines...and
make sure that the lines are 16" oc.as far as 1 1/2" vs 2", I think you would be
fine. from the gba article: R-7.5 for 2x4 walls; R-11.25 for 2x6 wallsyou do understand now that by doing this
more efficient wall & spending extra time $$
& labor that the trade off is smaller hvac system?
you'll need an accurate load calc.
you should start planning for this now as you'll
more than likely have to get several bids.
talk to pros @ hvac-talk.com great info there!btw...my SO's son lives in Minn. I've visited only
once, but SO flies up there farily often to help
son diy. the closed cell sealed the rim joist
in son's basement, bumped out roof to
add master bedroom suite & study.
SO talks son thru remodel projects...best of luck.
energy_rater_la
10 years agoPS...after talking with SO..
hardi will follow the profile of the wall.
if the studs are not straight the
hardi will show these imperfections.it isn't so much what is on the wall's
exterior as it is the studs themselves.run string lines...that will tell the tale.
kwoody51
Original Author10 years agoThanks for the additional info!
As for the vapor barrier between the drywall and the studs, this is where I get confused! I'm following what you said, but reading the below link, page 14 http://www.buildingscience.com/documents/guides-and-manuals/gm-guide-insulating-sheathing
The information says in cold climates you still want/ need a vapor barrier on the interior as you are trying to prevent the interior warm moist air from escaping into the wall cavity.
Quote from the article
As a general rule for standard framed construction, the vapor retarding layer should be placed to the interior of the assembly in cold climates (reducing the water vapor
from the higher humidity interior air from diffusing into the assembly).
While in hot humid climates, the
vapor retarding layer should be placed to the exterior of the assembly (reducing the water vapor from the
hot humid outside air from diffusing into the assembly).If you are in LA and I'm in MN I could see how your method of using the XPS as the vapor barrier would completely fine. However may not be the case for me in MN.
As for sizing the HVAC, I asked the builder about this and he said probably don't have to reduce the size... I follow your logic and may have to consult on this some more.
kwoody51
Original Author10 years agoIt also seems, from reading the same link (page 16-18) posted that even with 2" of XPS preventing the condensation on the sheathing, during winter months, its not achievable in MN. Thus adding an interior vapor/ air barrier is required/ recommended.
Based on this I'll probably just have the builder quote me 1" or on 1.5" and call it a day.
juline17
10 years agoI will not claim that I understand dew point calculations, however, with 1-1.5" of XPS, wouldn't there be condensation on the interior side of the foam?? If so, how is this handled?
kwoody51
Original Author10 years agoIn my situation there would be house wrap over the lab. So if there was condensation it would be between the XPS and the housewrap. Thus the house wrap would handle it.
kwoody51
Original Author10 years agoHeard back from the builder
~$10k+ for installing XPS
Need 190 sheets and ~100 hours of labor at $45/hour.Even if the sheets were free it would cost almost as much for XPS. I'm a bit surprised as is the builder. But I guess we have a lot of wall area with 10' ceilings.
So... Do I do closed cell spray or just blown insulation in the walls?!
energy_rater_la
10 years agoDoes that price sound out of line to you Worthy??
kwoody, time to get an actual bid for spray foam.
as I've said before I doubt that $5500 is for
walls & attic (roofline or attic floor...who knows??).get some bids that describe in detail what
they will provide.best of luck.
kwoody51
Original Author10 years agoThe $5500 is only the walls. 3" deep giving ~r-21.
They are going to spray foam the 2 rom joists and 2" of foam on the ceiling, this is built into the existing insulation quote.
I have some other quotes from spray foam companies coming in. While I don't not trust my builder I always feels better about having my own quotes for comparison. Just for example like this!
robin0919
10 years agoKw. $45/hr for LABOR????? That's 'outrageous'!! It must be union in your area!! As for the HVAC guys, they are used to using the X method that they have always used to maximize their profit and it usually sc@ews the customer. Make sure you have a manual J and blower door test done to get accurate measurements. Find someone like energy-rater in your area. She might be a member of a forum in this area and can recommend someone in your area.
energy_rater_la
10 years ago2" in rim joists should really be 3".
2" of foam on ceiling..clarify please
is this like on the attic floor & blown or
batts to be added over foam?
otherwise 2" isn't anything..big R-7
at BEST.
if it is 2" on roofline...what is that
supposed to achieve? it just isn't clear...to me
what is being offered.keep in mind with foam companies part of
the charge is built in for time to set up, mix
to heat & hoses to heat up. the extra product
(ie 3" vs 2") is just that ...product.
doubling the amount of product doesn't
double price. If foam co is being honest with
you.shop around.
I doubt 100 hours labor, 3 guys @ $15 each
shouldn't take a week and a half to install
sheathing.
builder probably did quick calc of $x for foam
sheathing = $xx X 2 for labor = 10k.in my area no one uses foam sheathing over
1" thick, so I don't know costs of thicker foam
sheathing. but do some price checking.best of luck
kwoody51
Original Author10 years agoThanks for the additional info!
100 hour of labor at $45/ hour is based off of the framing crew he's using, which he uses for ~95% of his jobs. They have to hang 190 sheets and build out the window frames. So I don't doubt it would take 4 guys a bit of time to doâ¦.
I agree the labor cost does seem a little high.Materials = 190*$15/ 1" sheet = $2850
Labor = $4500
Cost = $7350 (so not the $10k) but still more than the CC foam in the wallsThe 2" CC foam will be sprayed on the ceiling to act as an air seal and provide some R value. Blown fiberglass will be added on top of the CC foam to achieve R-50 in the ceiling.
Not saying it's dead but spending ~$7500⦠even with a 10-15% reduction in utilities doesn't seem to have an ROI that is worth the added cost.
kwoody51
Original Author10 years agoGot another quote back for spray foam. I asked them for 2 quotes -
just as my builder has it currently spec'd out
doing an entire spray foam jobDifference to add the spray foam to the wall - ~$6300.
So $5500 isn't out of line with this. This quote assume 3" in all the wall cavities.
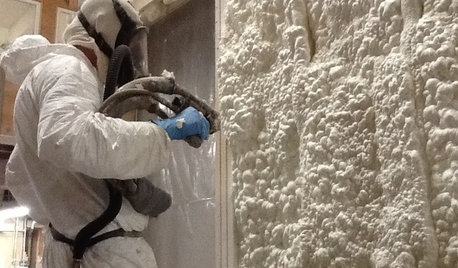
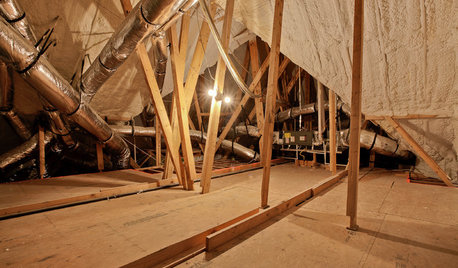
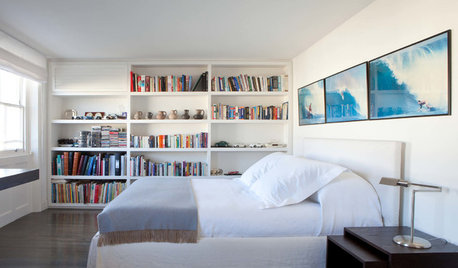
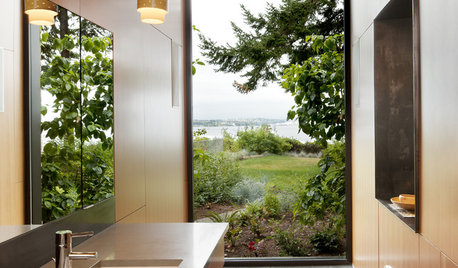
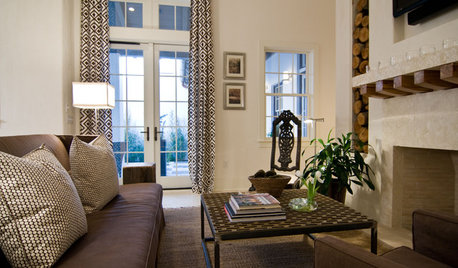
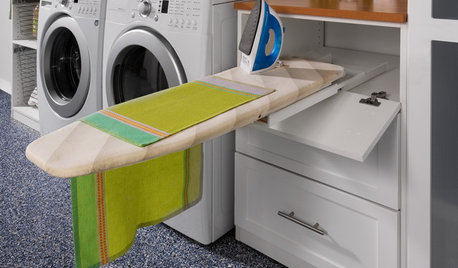
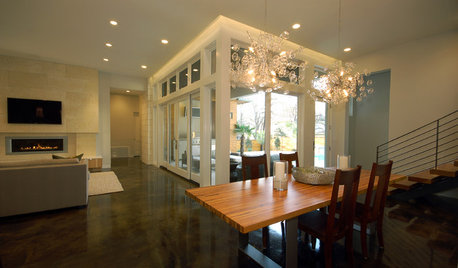
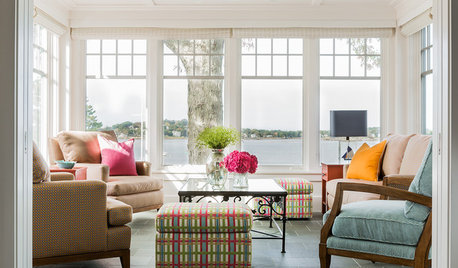
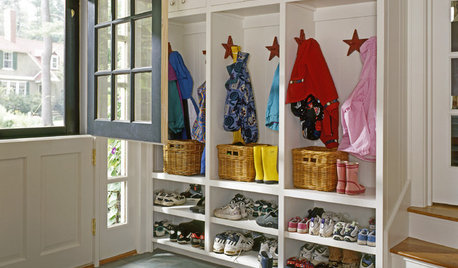
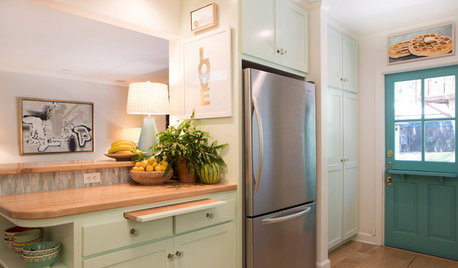
energy_rater_la