Got a new coil last month, now its not cooling again...
cgl102770
16 years ago
Related Stories

LIFEA Month-by-Month Guide to ‘Downton Abbey’ Withdrawal
Missing Lady Grantham’s zingers? Edith’s furrowed brow? Romance simmering downstairs? Here’s help to get you through until season 6
Full Story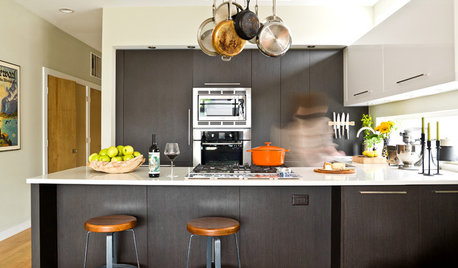
HOUSEKEEPINGHow to Clean Your Cookware So It Lasts
Avoid damage during everyday cleaning and stain scrubbing, with these tips for pots and pans made of popular materials
Full Story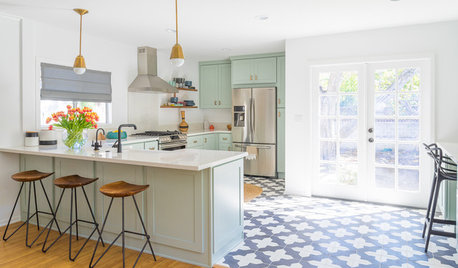
KITCHEN DESIGNTrending Now: 25 Kitchen Photos Houzzers Can’t Get Enough Of
Use the kitchens that have been added to the most ideabooks in the last few months to inspire your dream project
Full Story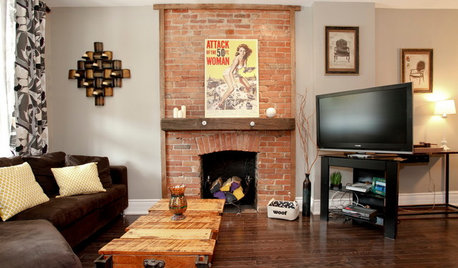
HOUZZ TOURSHouzz Tour: Totally New Beauty for a Townhouse in Just 5 Months
Hardworking contractors and loved ones help a Canadian Realtor put a run-down house on the fast track to charm
Full Story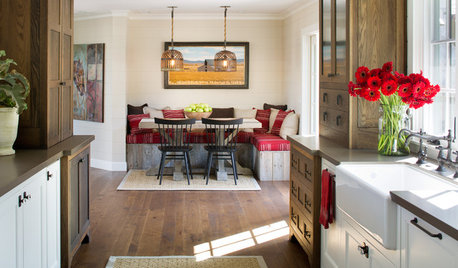
KITCHEN DESIGN15 Farmhouse Kitchens That Made Us Swoon This Month
Raw wood, natural light, shiplap siding — we just couldn’t get enough of these farmhouse-style kitchens uploaded to Houzz in January
Full Story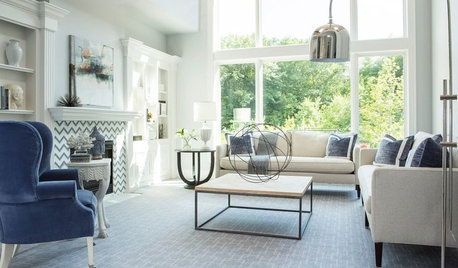
REMODELING GUIDES11 Reasons to Love Wall-to-Wall Carpeting Again
Is it time to kick the hard stuff? Your feet, wallet and downstairs neighbors may be nodding
Full Story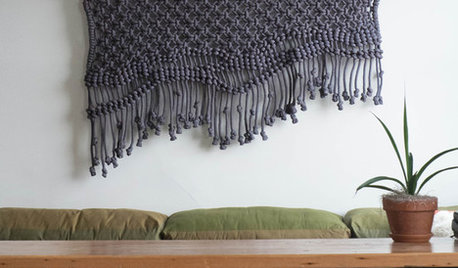
DECORATING GUIDESKnot Again! Macrame Is Back
It's happened. A craft that typified 1970s style (the owls, the spider plants!) is back, but better
Full Story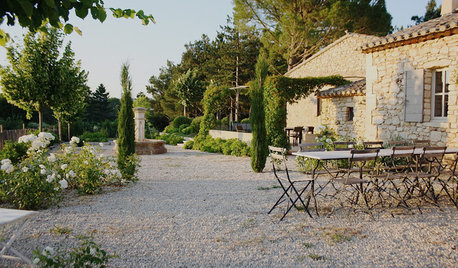
TRADITIONAL HOMESMy Houzz: A Centuries-Old French Estate Charms Again
Time and local artisans help a couple realize an idyllic French country retreat — and you can rent it
Full Story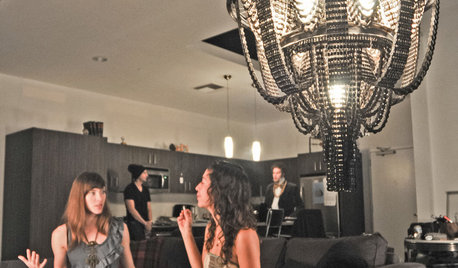
SALVAGEBike-Chain Chandeliers You've Got to See
Take a video ride with us to see how an artist creates amazing lighting fixtures solely from bike parts
Full Story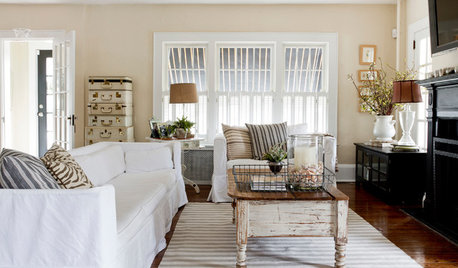
FEEL-GOOD HOMESimple Pleasures: 10 Ideas for a Buy-Less Month
Save money without feeling pinched by taking advantage of free resources and your own ingenuity
Full Story
deweymn
bob_brown
Related Professionals
Brentwood Los Angeles Solar Energy Systems · Fort Lee Solar Energy Systems · Greenwich Solar Energy Systems · Randolph Solar Energy Systems · Shelton Solar Energy Systems · Rosamond Solar Energy Systems · Laguna Hills Home Automation & Home Media · Park Ridge Home Automation & Home Media · Roselle Home Automation & Home Media · Stamford Home Automation & Home Media · Thornton Home Automation & Home Media · South Euclid Home Automation & Home Media · Seaside Fireplaces · Atascocita Fireplaces · Crestwood Fireplacescgl102770Original Author
daddo
deweymn
daddo
bob_brown
ckmb5150
deweymn
daddo
cgl102770Original Author
deweymn