48" Range Rear wall clearance help fred s?
Drewski 22785
5 years ago
Related Stories
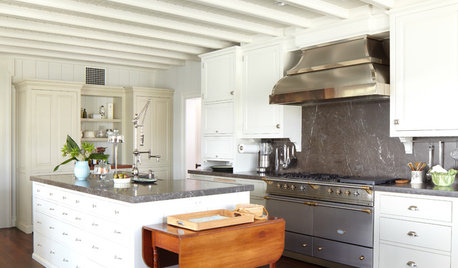
KITCHEN DESIGNHow to Find the Right Range for Your Kitchen
Range style is mostly a matter of personal taste. This full course of possibilities can help you find the right appliance to match yours
Full Story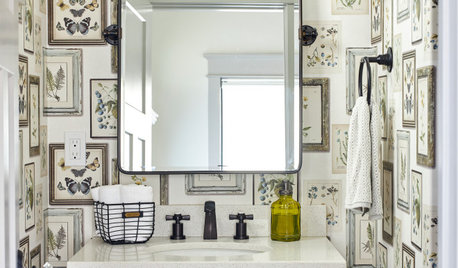
BATHROOM DESIGNKey Measurements to Help You Design a Powder Room
Clearances, codes and coordination are critical in small spaces such as a powder room. Here’s what you should know
Full Story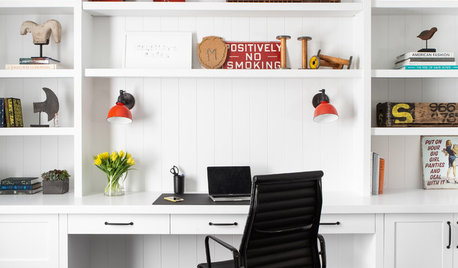
REMODELING GUIDESKey Measurements to Help You Design the Perfect Home Office
Fit all your work surfaces, equipment and storage with comfortable clearances by keeping these dimensions in mind
Full Story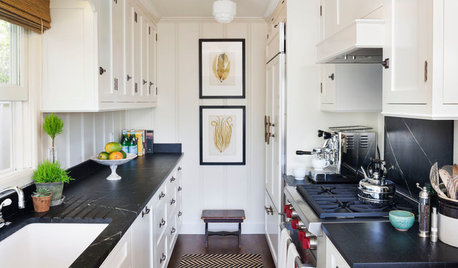
KITCHEN DESIGNWhy a Designer Kept Her Kitchen Walls
Closed kitchens help hide messes (and smells) and create a zone for ‘me time.’ Do you like your kitchen open or closed?
Full Story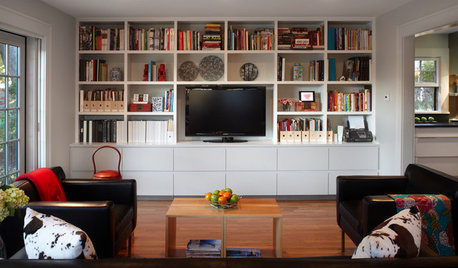
GREAT HOME PROJECTSHow to Get That Built-in Media Wall You Really Want
New project for a new year: Tame clutter and get a more stylish display with a media unit designed to fit your space just right
Full Story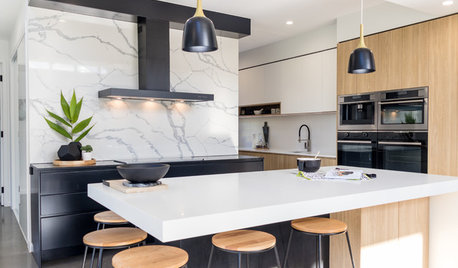
KITCHEN DESIGNHow to Get Your Range Hood Right
Get a handle on the technical specs, and then learn about fun design options for creating a beautiful kitchen feature
Full Story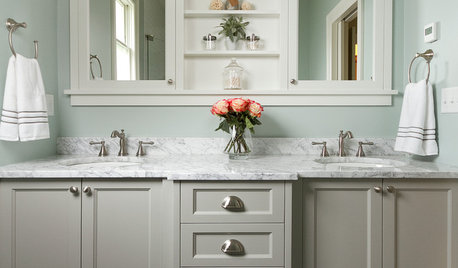
BATHROOM DESIGNShould You Get a Recessed or Wall-Mounted Medicine Cabinet?
Here’s what you need to know to pick the right bathroom medicine cabinet and get it installed
Full Story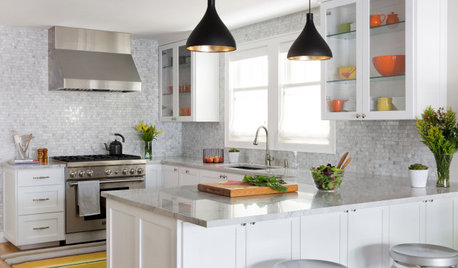
KITCHEN DESIGNKey Measurements to Help You Design Your Kitchen
Get the ideal kitchen setup by understanding spatial relationships, building dimensions and work zones
Full Story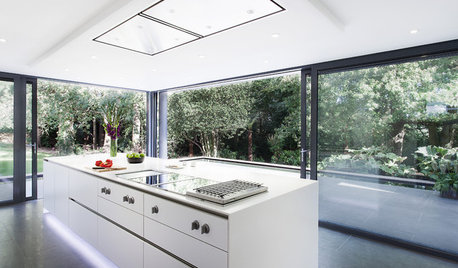
KITCHEN APPLIANCESDisappearing Range Hoods: A New Trend?
Concealed exhaust fans cut visual clutter in the kitchen
Full Story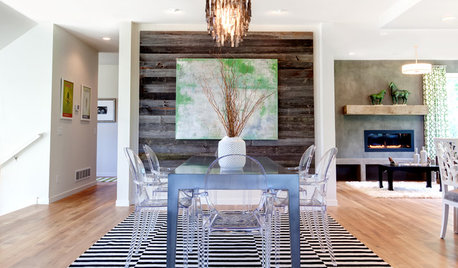
GREAT HOME PROJECTSWhat to Know About Adding a Reclaimed-Wood Wall
Here’s advice on where to put it, how to find and select wood, what it might cost and how to get it done
Full Story
Patricia Colwell Consulting
Drewski 22785Original Author
kaseki
Drewski 22785Original Author
live_wire_oak
catinthehat
Drewski 22785Original Author
catinthehat
User
Drewski 22785Original Author
kaseki
catinthehat