Building my own house! Will need advice as I go!
DFW Rusty
4 years ago
Featured Answer
Sort by:Oldest
Comments (92)
DFW Rusty
4 years agoUser
4 years agolast modified: 4 years agoRelated Professionals
Norco Home Builders · Troutdale Home Builders · Anchorage General Contractors · Cape Girardeau General Contractors · Cheney General Contractors · Del Aire General Contractors · North New Hyde Park General Contractors · Rocky Point General Contractors · Danbury Flooring Contractors · North Tustin Flooring Contractors · Southlake Flooring Contractors · Sun City Flooring Contractors · Superior Flooring Contractors · Wixom Flooring Contractors · Honolulu Siding & ExteriorsDFW Rusty
4 years agoVirgil Carter Fine Art
4 years agoDFW Rusty
4 years agoDFW Rusty
4 years agoDFW Rusty
4 years agolast modified: 4 years agoDFW Rusty
4 years agoDFW Rusty
4 years agoDFW Rusty
4 years agoSeabornman
4 years agoCyndy
4 years agoDFW Rusty
4 years agoA B
4 years agoMark Bischak, Architect
4 years agoworthy
4 years agolast modified: 4 years agoDFW Rusty
4 years agolast modified: 4 years agoDFW Rusty
4 years agoDFW Rusty
4 years agoDFW Rusty
4 years agolast modified: 4 years agoworthy
4 years agolast modified: 4 years agoHALLETT & Co.
4 years agoDFW Rusty
4 years agoDFW Rusty
4 years agolast modified: 4 years agoDFW Rusty
4 years agolast modified: 4 years agoDFW Rusty
4 years agoMinnesota Inspections LLC
4 years agoDFW Rusty
4 years agoDFW Rusty
4 years agoUser
4 years agoDFW Rusty
4 years agoUser
4 years agoDFW Rusty
4 years agoKitchen Tune-up Zeeland, Sales & Design
4 years agoDFW Rusty
4 years agoMinnesota Inspections LLC
4 years agoSeabornman
4 years agoMinnesota Inspections LLC
4 years agoMinnesota Inspections LLC
4 years agoCheryl Hannebauer
4 years agoProSource Memphis
4 years agoCheryl Hannebauer
4 years agobry911
4 years agolast modified: 4 years agoLynn Heins
4 years agoDFW Rusty
4 years agoDFW Rusty
4 years agoMinnesota Inspections LLC
4 years agoDFW Rusty
4 years agolast modified: 4 years agobry911
4 years agoworthy
4 years agolast modified: 4 years ago
Related Stories
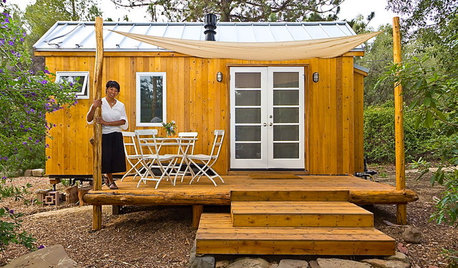
LIFEYou Said It: ‘Just Because I’m Tiny Doesn’t Mean I Don’t Go Big’
Changing things up with space, color and paint dominated the design conversations this week
Full Story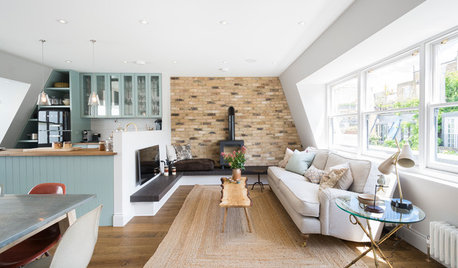
REMODELING GUIDESWhere Do I Start When Renovating My House?
Eager to get going on a project but not sure where to begin? Read this practical guide to getting started
Full Story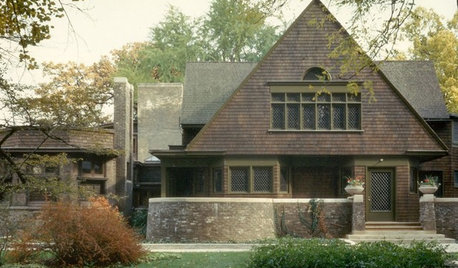
FRANK LLOYD WRIGHTWhat Frank Lloyd Wright's Own House Tells Us
The buildings dreamed up here changed the course of architecture — and Wright's home was no less a design lab than the studio itself
Full Story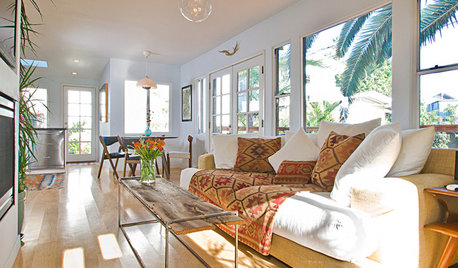
LIFEYou Said It: ‘I Actually Prefer Small Houses’ and Other Quotables
Design advice, inspiration and observations that struck a chord this week
Full Story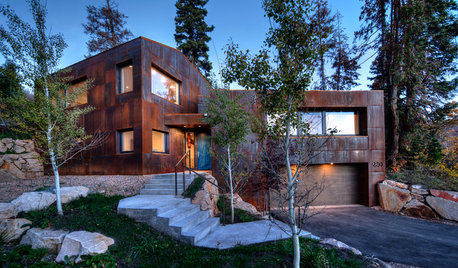
GREEN BUILDINGArchitects Design Their Own Passive Houses
To learn more about the techniques, these pros designed and built these energy-efficient homes for their own families
Full Story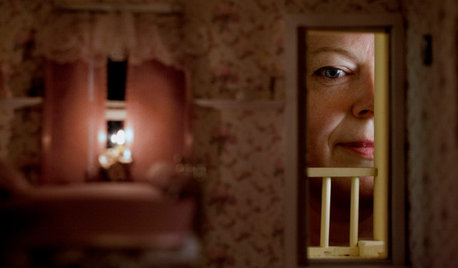
FUN HOUZZHow to Build a Really, Really Small House
A four-minute film holds the magnifying glass up to a dollhouse collector smitten with all things small
Full Story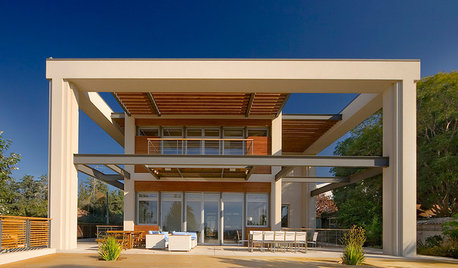
REMODELING GUIDESNesting Boxes: Houses With Homes of Their Own
Framing one box with another creates a whole new style of modern indoor-outdoor living
Full Story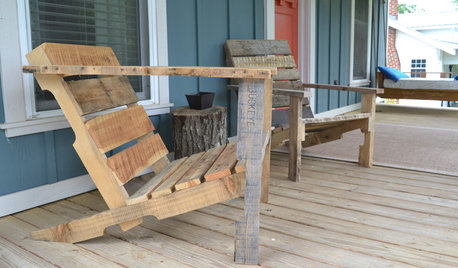
WOODWORKINGBuild Your Own Wooden Deck Chair From a Pallet — for $10!
Take the ecofriendly high road with a low-cost outdoor chair you make yourself
Full Story
GREEN BUILDINGWhy You Might Want to Build a House of Straw
Straw bales are cheap, easy to find and DIY-friendly. Get the basics on building with this renewable, ecofriendly material
Full Story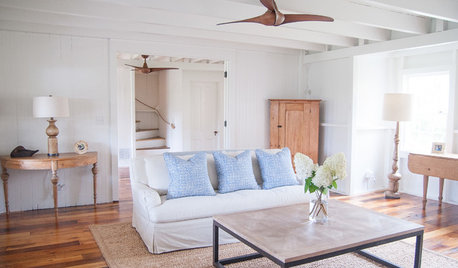
HOUZZ TOURSHouzz Tour: A Connecticut Beach House Builds New Memories
Extensive renovations make an 8-bedroom summer home ready for a family and many guests
Full StoryMore Discussions
DFW RustyOriginal Author